Update June 2025
The residential construction industry in Australia has faced ongoing criticism over build quality and workmanship issues. Many new homes are plagued with problems that significantly impact owners, from minor defects to major structural issues.
What’s going wrong?
A big part of the problem lies in a lack of proper skills and training. The industry relies heavily on subcontractors and labourers with little experience in building homes. They often don’t fully understand building materials, standards and regulations. Corners get cut to save time and money.
Quality control is sorely lacking. Inadequate supervision, inspection and testing mean faults go unnoticed until it’s too late. The “she’ll be right” attitude prevails over a desire to achieve high quality and meet contractual obligations.
The boom-bust cycle of residential construction encourages a “get in, get out” mindset. Builders rush to complete homes as quickly as possible to capitalise during busy periods, with little regard for longevity or performance.
Home owners are left dealing with the fallout from leaking roofs, water damage, electrical faults, and structural issues. The cost to repair these problems falls on owners, not the companies responsible for poor workmanship.
It’s clear the industry needs an overhaul to improve standards. Stricter regulations, better training, and more robust quality control measures are essential.
Builders should focus on high quality and meeting the reasonable expectations of home owners, not just speed and profits.
Until there’s real change, new home buyers in Australia will continue to face an uncertain future with their most valuable asset.
Causes of Poor Workmanship in Residential Construction
The root causes of poor workmanship in residential construction are complex but often come down to a lack of skill, experience, proper training, and professionalism.
Many workers enter and exit the industry rapidly, not developing strong competencies or a sense of craftsmanship. They may lack a solid understanding of building materials, construction methods and safety standards. Without proper supervision, training and quality control, poor practises become normalised and quality suffers.
Corners are frequently cut to save time and money, sacrificing longevity and performance. The “rip shit and bust” mentality focuses on speed over quality, getting jobs done as quickly as possible. Proper building inspections are bypassed, and subpar work is covered up.
Workers may lack professional pride in their work and see residential construction as merely a job, not a craft. They have little incentive to go above and beyond or continuously improve their skills. Many do not seem to grasp the impact of their work on people’s lives and finances.
To improve, the industry needs stronger regulation and enforcement of standards, better training, and a culture shift to value quality and craftsmanship. Supervisors should oversee projects closely, inspecting work at multiple stages. Workers need mentorship and a chance to develop expertise over the long-term.
Home owners also must be educated on what constitutes good workmanship so they can identify issues early on. By demanding higher quality and being willing to pay for it, they can motivate builders to make positive changes. With a more professional, skilled workforce that takes pride in their craft, residential construction quality in Australia would see vast improvements.
Lack of Understanding of Materials and Building Standards
The residential construction industry in Australia has faced criticism over the lack of understanding of building materials and standards. Many builders and tradespeople do not have a strong grasp of how different materials work, their limitations, and how they interact. They also struggle to keep up with the constant changes in building codes and regulations.
For example, waterproofing measures are frequently done incorrectly or overlooked altogether. Many builders do not fully understand how to properly seal wet areas like bathrooms, laundries, and balconies to prevent leaks and water damage. The recent updates to AS3740 make clear through the details of this update, that the associations and regulatory bodies acknowledge the poor level of workmanship and are changing standards to mandate better performance requirements.
Part of the problem stems from a lack of proper training and education. The “have-a-go” attitude of some builders means that people enter the trade without formal qualifications or apprenticeships.
They learn on the job without fully understanding the technical aspects of the work. Even for qualified tradespeople, continuous learning is needed to keep skills and knowledge up to date, but this often falls by the wayside in favour of getting jobs done quickly.
Builders and developers should place more importance on technical expertise and professional development. Additional training on building materials, construction techniques, standards compliance and quality control processes is essential. Mentoring programmes where experienced builders pass on knowledge to new tradespeople could also help address the skills shortage.
Home owners also need to take more responsibility for the quality of work done on their properties. Do thorough research on builders before hiring them, check their qualifications, experience and references from previous clients.
Closely supervise work as it progresses and do not be afraid to speak up if something does not seem right.
Paying attention to the details during construction can help avoid major quality issues down the road.
With improved education, a commitment to continuous learning, and more active participation from home owners, the standard of residential construction in Australia can be lifted to provide safer, higher quality homes.
Lack of basic business acumen
Many trades and contractors often struggle with basic business processes. Let me illustrate this with an example: invoicing. Sometimes, tradespeople don't grasp the connection between a Purchase Order and a Tax Invoice, and they might not know what to include on a tax invoice. As they expand their businesses to serve more customers, they often neglect to improve their business processes.
Here's a recent experience I had. I hired a plumber to fix another plumber's mistakes. Since it was our first time working with them, we didn't issue a purchase order. We simply discussed the work scope over the phone, which was quite straightforward - inspect the installation and bring it in line with the manufacturer's recommendations. After completing the job, we received an invoice, which we promptly paid. However, a few days later, we got a second invoice for additional work. We hadn't asked for or discussed any extra work. To make things more confusing, the contractor's office referenced an outdated law, the Building & Construction Industry Payment Act (BCIPA), on their invoice. This act was replaced by the Building Industry Fairness (Security of Payment) Act in 2017. This shows that the contractor isn't up-to-date with current laws. Because we were aware of the changes, we had to spend an hour researching and preparing a payment schedule to respond to their payment claim to be Act compliant.
Such inefficiencies waste human resources and can be attributed in part to a lack of business acumen and failure to keep up with current standards. Just imagine the impact of sending out ten incorrect invoices every week - it translates to nearly $1000 in wasted worker productivity. This is one area of a business, it is not unreasonable to assume that they make similar mistakes in other areas, installation, quality management, maintenance, communication, planning, book keeping, human resources.
It really confounds me that people start making money in their chosen profession, then tune out to the fact that they could be making so much more if they only started to review how they do what they do and identify bottlenecks (see note below), waste, and inefficiencies rather than blame everyone else and waste the time of others. Ultimately, someone bears the cost of this inefficiency, and that someone is the consumer.
Note: if you are interested in this management principle its called the "Theory of constraints" and our other blog post FOUND HERE.
The Need for Improved Training and Skills
The residential construction industry in Australia is in dire need of improved training and skills. Many issues stem from a lack of proper education and development.
To start, technical schools and apprenticeship programmes should place more emphasis on understanding materials and building standards. Tradespeople need to know how different materials work, interact and perform over time. They should understand not just how to install something, but why it’s installed that way.
Building codes and Australian Standards change regularly, so continuous learning should be mandatory. It is our opinion that to keep and maintain a license, you must complete refresher courses/modules every year and submit a certificate of competency to be granted your license for another 12-month period.
Contractors and tradespeople should also improve soft skills like communication, problem-solving, and critical thinking. Residential construction involves coordinating many moving parts, so the ability to work with others in a professional manner is essential. Tradespeople must be able to interpret plans, evaluate issues, and make good decisions on the fly.
Site supervisors play an integral role in quality management, so they require both technical and soft skills to properly oversee projects. They need to monitor workmanship, ensure inspections are done, and make sure key milestones are met on schedule without sacrificing quality. Supervisors should take responsibility for the overall outcome, not just productivity.
To address these needs, governments and industry groups should incentivise more young people to pursue construction careers through scholarships, grants and co-op programmes. They should promote construction as a viable long-term career, not just a job.
For existing workers, subsidised or mandatory ongoing education and skills training should be required. Both technical and soft skills courses would help address knowledge gaps and encourage a more professional mindset focused on quality and best practises.
Improving education, skills and attitudes across the residential construction sector will help build a workforce capable of delivering high-quality homes that stand the test of time. Home owners will benefit from safer, more durable housing, and builders will benefit from higher customer satisfaction and fewer call-backs or legal issues. Investing in human capital is key.
Balancing Speed and Quality in Construction Projects
Speed and quality are often at odds in residential construction. Project managers are under pressure to complete homes as quickly as possible to maximise profits, but this can compromise quality. Home owners end up paying the price for shoddy workmanship and subpar materials that don’t stand the test of time.
Rushing Critical Stages
When construction is rushed, important stages like concrete pouring, framing, and waterproofing can be compromised. Concrete needs time to properly cure and reach maximum strength. Framing needs to be carefully measured, cut, and secured for structural integrity. Waterproofing requires meticulous application of sealants to avoid leaks. Skimping on any of these to save time often leads to problems down the road.
Lack of Supervision
Project managers focused on speed may not properly oversee tradespeople and subcontractors. Without vigilant supervision, mistakes and cut corners are more likely to go unnoticed. Tradespeople may take shortcuts to move quickly between jobs, leading to issues like pipes installed at improper angles, loose wiring, uneven flooring, or uneven paint coverage.
Low-Quality Materials
Inferior, low-cost materials are more prone to failure and deterioration. They may not withstand environmental stresses or normal wear and tear. Roofing, flashings, cladding, the use of MDF products, and other cheap/not fit for longevity materials that cut corners to reduce costs often need early replacement, costing home owners time and money.
For improved residential construction quality, balance is key. Project schedules should allow adequate time for each stage of construction and proper supervision. Quality, durable materials, even if more expensive upfront, save money and headaches over the lifetime of the home. With oversight, accountability, and a commitment to excellence, home builders can achieve sustainable, energy-efficient houses that stand the test of time.
Implementing Effective Quality Control Processes
To achieve high quality in residential construction, effective quality control processes must be implemented at every stage. Quality control refers to the steps taken to ensure workmanship, materials, and final results meet expected standards.
For home builders, this means:
Inspections
Conducting regular inspections of work in progress and upon completion. Inspectors should check that construction aligns with building codes, regulations, and best practises. They examine everything from foundations and framing to electrical wiring, plumbing, and insulation. Inspections help catch mistakes early and ensure safety, functionality, and durability.
Supervision
Providing adequate supervision of contractors and tradespeople. Supervisors oversee day-to-day work, answer questions, and make sure tasks are performed properly. They have technical knowledge about how materials, tools, and techniques should be applied. Supervision helps uphold high standards of workmanship and compliance.
Testing
Performing necessary testing to verify quality. This includes testing building materials to confirm they meet specifications, as well as testing components like plumbing, electrical systems, and HVAC once installed. Testing helps identify any faults so they can be addressed before final inspection.
Documentation
Maintaining thorough documentation of the entire build process. This means keeping records of permits, plans, changes, inspections, test results, materials used, and more. Complete documentation provides transparency and accountability, allowing quality to be tracked and improved over time.
Implementing these quality control processes requires a commitment to professionalism, continuous improvement, and building homes that stand the test of time. Shortcuts might speed up construction, but they compromise safety, functionality, and longevity. For home owners, quality control means peace of mind that their investment is sound. And for builders, it means establishing a reputation for excellence.
Fostering a Culture of Quality and Continuous Improvement
To improve residential construction quality in Australia, a culture of quality and continuous improvement must be fostered. This starts from the top, with companies and managers leading by example.
Promote Quality Over Quantity
Speed and volume have become priorities, with “rip, shit and bust” attitudes aiming to get in and out of projects as quickly as possible. This must change. Companies should focus on quality, not chasing bonuses for hitting volume targets. Managers should reward high quality work, not just fast work.
Invest in Training
Many issues stem from a lack of proper training, skill, and competence. Companies need to invest in ongoing training for workers to strengthen understanding of:
- Material properties and how to work with them
- Standards and building regulations
- Quality control procedures like supervision, inspection and testing
Continuous Improvement
A desire to continuously improve standards and skills without compromising quality or obligations is key. Workers and companies should:
- Review issues from past projects and make improvements
- Stay up to date with the latest products, methods and regulations
- Provide mentorship and learning opportunities for new workers
- Welcome feedback and make changes to address concerns
Foster Responsibility
All parties must take responsibility for quality - from architects and engineers to tradespeople, supervisors and building surveyors. A professional attitude where people take pride in high quality work is needed. Blaming others when issues arise must end.
Promoting collaboration, communication and a shared vision of excellence can help transform residential construction in Australia. It will take time, but by investing in skills, responsibility and a culture where quality is valued over quantity, the industry can build a better future.
Moving Away From the "Rip, Ship and Bust" Mentality
The “rip, ship and bust” mentality that has plagued parts of the Australian residential construction industry refers to the tendency for some builders and tradespeople to cut corners in order to finish jobs as quickly as possible.
Many tradesmen enter the industry with the goal of making fast money, with little concern for building quality, workmanship or client satisfaction.
They aim to get in, make a profit, and get out as quickly as possible before problems arise or their poor practises catch up to them.
This attitude leads to shoddy, substandard work that significantly reduces the lifespan and value of homes. Common issues include:
- Poor waterproofing and insulation leading to leaks, mould and high energy bills.
- Faulty wiring and plumbing that requires expensive repairs.
- Structural issues due to improper construction methods.
- Use of cheap, unsuitable materials that deteriorate quickly.
The effects are felt for years by home owners in the form of high maintenance costs, health issues and difficulty selling their properties. Builders with this mentality have little incentive to change as they face few consequences, often dissolving their companies to avoid accountability before starting a new one.
To remedy this, stronger licensing and accreditation requirements are needed to weed out dodgy builders. Home owners should do thorough research on builders, check reviews and references, and consider getting an independent building inspection during construction.
Most of all, we must work to remove the stigma around residential construction as a “get rich quick” scheme, and build a culture where quality, safety, and customer satisfaction are prioritised. With improved education, standards and oversight, we can transform an industry plagued by a “rip, ship and bust” mentality into one focused on integrity, excellence and longevity.
Construction Quality Management FAQs
Many people have questions about construction quality management in Australia and how it can be improved. Here are some of the most frequently asked questions and their answers:
What are the main causes of poor quality in residential construction?
Some of the major factors contributing to quality issues include:
- Lack of proper training, skill and experience. Many workers enter the industry with little experience or formal qualifications.
- Poor workmanship and cutting corners to save time. There is pressure to complete projects quickly, often at the expense of quality.
- Lack of understanding about materials, standards and building regulations. Workers may not fully grasp how materials should be installed or the reasons behind certain standards.
- Inadequate quality control and supervision. Insufficient oversight means mistakes and substandard work are not identified and rectified.
- Focus on speed over quality. The desire to finish jobs rapidly and move on to the next one can compromise building quality.
How can quality management in residential construction be improved?
Several steps can be taken to enhance quality management:
- Improved training, education and licencing of workers. This will increase understanding of proper techniques, materials and standards.
- Stricter quality control measures including more thorough inspections and testing (ITP are an easy way to do this). This helps identify issues early so they can be addressed.
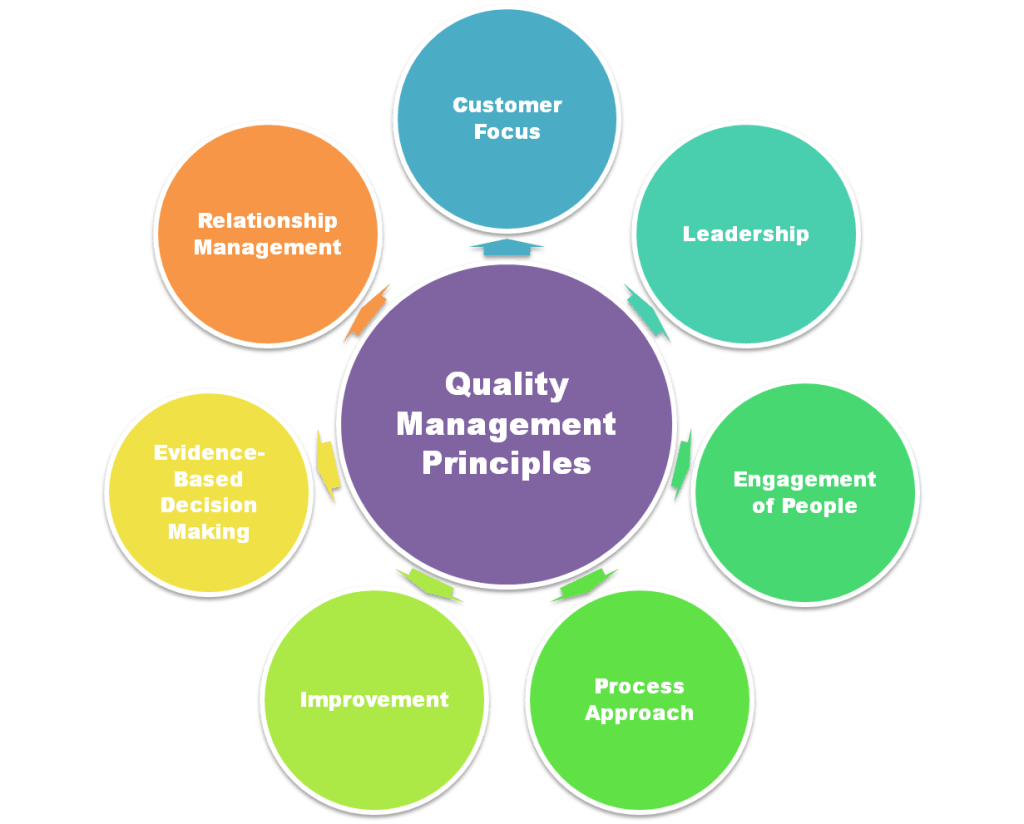
- Shift attitudes to value high quality and customer satisfaction over quick completion of projects. This may require a cultural change within parts of the industry.
- Increase supervision and accountability. Workers and contractors need to be monitored more closely to ensure compliance with standards. Penalties can be imposed if quality is compromised.
- Review and update building standards and regulations. Outdated or insufficient standards do not encourage best practises and quality outcomes. Regular reviews and updates are needed.
- Promote a desire for continuous improvement. All parties should aim to constantly enhance quality through ongoing education, adopting innovative practises and learning from past mistakes.
- Increase transparency and consumer protections. Home owners need access to quality ratings, histories of complaints, and avenues for pursuing remediation if quality issues arise. This also motivates improved quality.
Enforcement by regulatory authorities
The residential construction industry in Australia has faced significant criticism over quality and compliance issues in recent years. Government regulators aim to enforce higher standards to improve safety, sustainability and accountability.
Inspections and Penalties
Regulatory agencies conduct inspections of building sites to check for compliance with building codes and standards. Fines, stop-work orders, and licence suspensions can be issued for violations. The government has sought to increase penalties for serial offenders to motivate change.
While inspections aim to identify problems early, limited resources mean not all sites are inspected. Some issues may not become apparent until long after construction is complete. Home owners are often left dealing with the fallout of subpar workmanship and building practises. Additional inspections, tighter controls on licensing, and harsher penalties for dodgy operators are needed to weed out under-performing builders.
Education and Training
The skills and knowledge of tradespeople play a significant role in achieving quality construction. Programmes to improve training, apprenticeships, and continuing education for builders and subcontractors should be priorities. Upskilling the workforce will produce better outcomes and help change attitudes focused on maximising short-term profits.
Builders must keep up with advancements in materials, methods and technologies to meet energy efficiency targets and produce sustainable homes. They need a sound understanding of building standards and regulations to ensure compliance. Ongoing professional development should be mandatory to maintain licensing.
While enforcement and penalties serve an important purpose, a cooperative approach with industry is more likely to drive real change. The government and regulators should work with builders and trades associations to develop initiatives centred on education, skills development, and promoting a culture where quality and compliance are valued. The result will be safer, higher-quality homes and a construction sector focused on continuous improvement.
Conclusion
As home owners, don't accept shoddy, subpar workmanship that won't stand the test of time. Demand better from your builders and tradespeople. Hold them accountable to the National Construction Code and the Australian Standards.
And for those in the industry, take pride in your work, invest in ongoing training, focus on quality over speed, and build homes like you would want to live in yourself.
Australia's homes should be built to last, not fall apart after a few short years. It's time for a revolution in residential construction quality. The solutions are clear, now let's make it happen.