Introduction
Choosing the right framing timber is crucial in Australian residential construction, not only for structural integrity but also for cost-effectiveness and compliance with national standards. This blog post compares 90x35 MGP (Machine Graded Pine) timber framing with Laminated Veneer Lumber (LVL) framing, focusing on assembly, cost, quality, and construction time, all within the guidelines of the Australian Standard AS1684.2.
Overview of Timber Framing Materials
90x35 MGP Timber Framing
90x35 MGP timber is a popular choice for framing in Australian homes. It is made from machine-graded pine, which ensures consistent quality and strength. Its main use is in the structural framing of walls, floors, and roofs due to its reliability and cost-effectiveness.
LVL (Laminated Veneer Lumber) Framing
LVL is made by bonding together multiple layers of thin wood veneers under heat and pressure, creating a product that is stronger and more consistent than traditional lumber. It is often used for beams, lintels, and other structural components where higher strength and stiffness are required.
Choosing the right material affects not only the durability and cost of the construction but also its compliance with the Australian Standard AS1684.2, which governs residential timber framing construction.
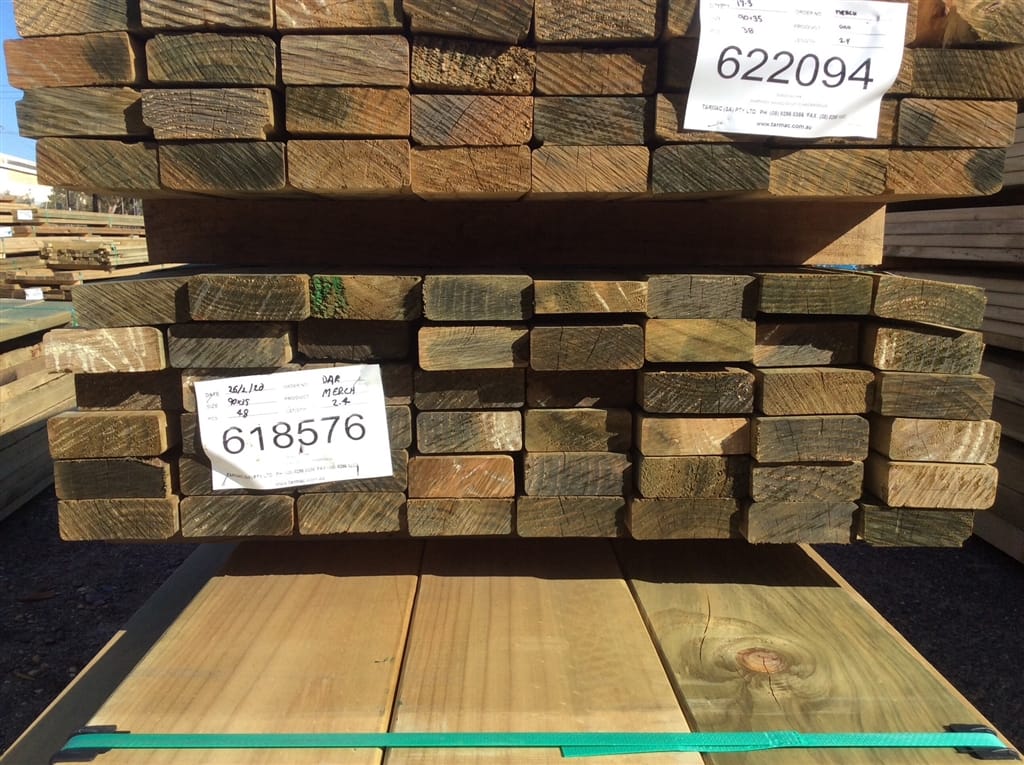
Comparative Analysis
Assembly and Installation
90x35 MGP Timber Framing is renowned for its straightforward installation process. Its lightweight nature allows for easy manipulation and cutting on-site, making it a preferred choice for projects with tight deadlines or limited labor resources. This ease of handling can significantly reduce the assembly time, making it an attractive option for many builders. However, despite its user-friendliness, it's crucial to ensure that MGP timber is correctly treated and installed to avoid future structural issues, especially in moisture-prone areas.
LVL (Laminated Veneer Lumber), while offering superior strength and stiffness, presents a different set of challenges in assembly and installation. Its heavier weight and the necessity for precise cutting mean that LVL often requires specialized equipment and skilled labor. This can increase the initial labor costs and extend the installation time. However, the material's consistent quality and strength can simplify the design process, potentially reducing the overall number of pieces needed and offsetting some of the additional labor requirements.
Cost
The cost aspect is multifaceted, involving initial outlay, long-term savings, and potential resale value implications. MGP timber is generally more affordable upfront, which can significantly influence budget-conscious decisions. It's an economical choice that doesn't compromise on quality, particularly for standard residential projects. However, potential future costs related to maintenance or repair due to environmental damage should be considered.
On the other hand, LVL's higher initial cost is justified by its enhanced durability and strength, which can lead to savings in the long term. Its resistance to warping, shrinking, and splitting reduces the need for replacements or repairs, making it a cost-effective option over the lifespan of a building. Furthermore, the use of LVL can contribute to a higher resale value of the property, thanks to its perceived quality and durability.
Quality and Durability
When it comes to quality and durability, both materials have their merits. MGP timber is subjected to rigorous grading processes, ensuring that it meets the structural standards required for residential construction. However, being a natural material, it can be vulnerable to environmental factors like moisture and termites, which could affect its longevity and performance over time.
LVL excels in uniformity and strength, engineered to resist environmental challenges more effectively than traditional timber. Its manufacturing process minimizes defects and inconsistencies, providing a high-quality, durable product that stands up well to Australia's varied climate conditions. This makes LVL an excellent choice for critical structural elements where reliability is paramount.
Construction Time
Construction timing is critical when deciding between these materials. Opting for MGP timber can speed up construction due to its easy handling and familiarity among tradespeople. This is especially important for projects with tight deadlines or significant labor cost concerns.
LVL may require a bit more time for cutting and assembly, but its ability to span longer distances and carry greater loads can reduce the overall number of structural components needed. This reduction can lead to fewer installations and connections, ultimately streamlining the construction process for complex or large-scale projects.
Compliance with AS1684.2
Adherence to the Australian Standard AS1684.2 is important for ensuring that residential constructions meet the required safety and performance criteria. MGP timber, widely used in Australian construction, aligns well with the standards outlined in AS1684.2, offering a reliable solution for most residential framing requirements. Its versatility and performance characteristics make it suitable for a broad range of applications, from wall and roof framing to floor systems.
LVL's design flexibility and superior load-bearing capacity also make it highly compatible with AS1684.2, particularly for applications requiring long spans or heavy loads. Its use can simplify the design and compliance process, offering architects and engineers greater creative freedom without compromising on safety or performance.
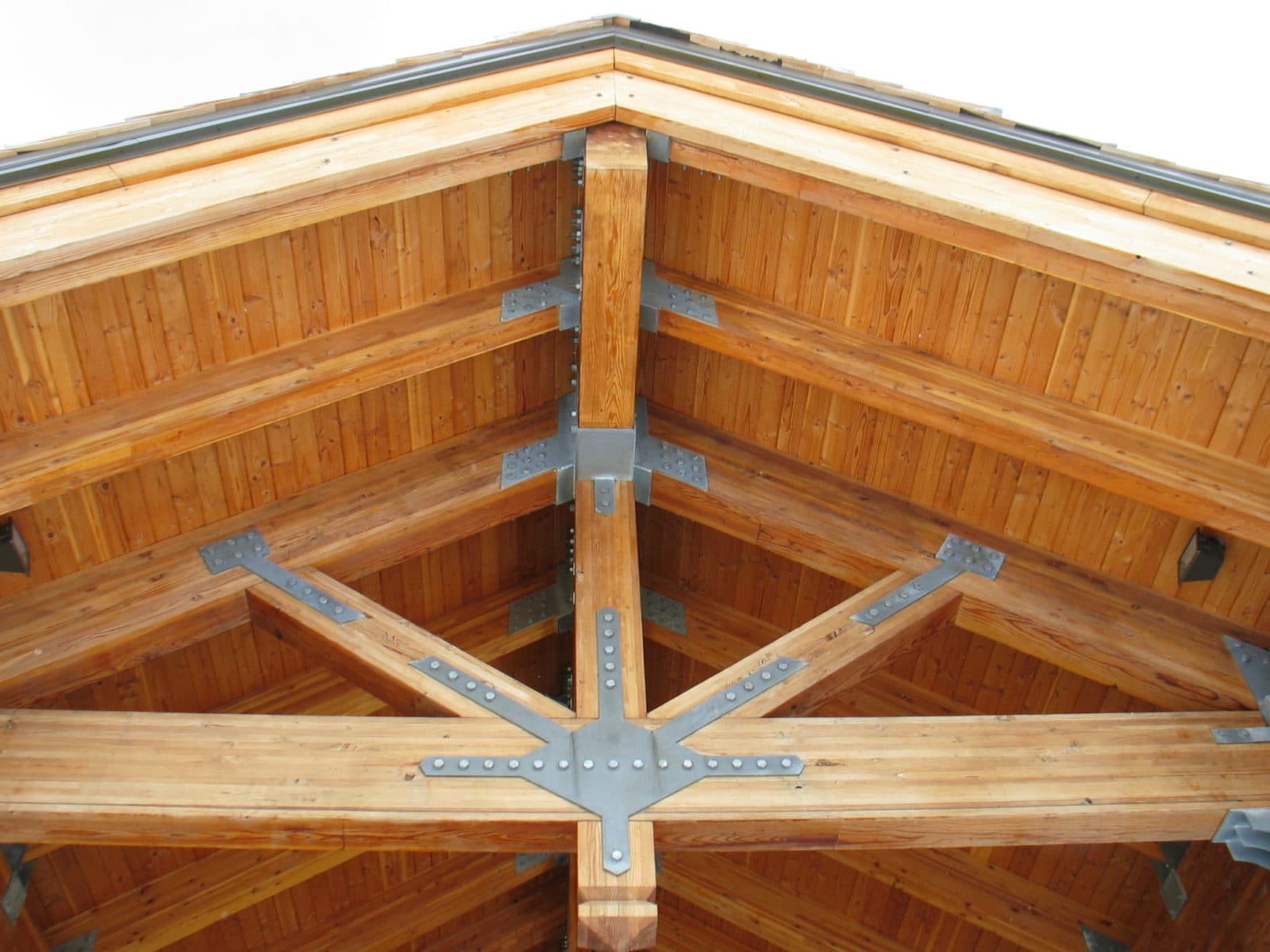
Environmental Impact and Sustainability
Choosing sustainable materials is increasingly important in today's construction landscape, especially for environmentally conscious homeowners. 90x35 MGP timber comes from pine plantations, where trees are grown specifically for timber production, offering a renewable resource when managed responsibly. Its production process is relatively energy-efficient, and it acts as a carbon sink, storing carbon dioxide throughout its lifecycle. However, the environmental impact can vary based on the distance the timber needs to be transported and the sustainability practices of the forestry operations.
Laminated Veneer Lumber (LVL) shares similar advantages, being made from wood, a renewable resource. Its manufacturing process allows for the use of smaller trees and minimizes waste by utilizing nearly every part of the tree. LVL's efficiency and strength mean that less material is needed to achieve the same structural capabilities, potentially reducing the overall environmental footprint. Yet, the adhesives and chemicals used in LVL production could have environmental implications, making the choice of suppliers with eco-friendly practices crucial.
Both materials can be part of a sustainable construction approach, especially when sourced from suppliers that adhere to certifications like the Forest Stewardship Council (FSC) or Programme for the Endorsement of Forest Certification (PEFC), which ensure the sustainable management of forests.
Energy Efficiency and Insulation Properties
The thermal performance of a home significantly affects its comfort and energy costs. Timber, in general, has good natural insulation properties due to its cellular structure, which traps air and slows the transfer of heat. 90x35 MGP timber, being a solid wood product, contributes positively to a home's energy efficiency by providing natural insulation. This can reduce reliance on heating and cooling systems, lowering energy bills and improving the home's overall energy footprint.
LVL is similarly effective in insulating properties, with the added benefit of creating tighter construction due to its dimensional stability and strength. This can further enhance a home's energy efficiency by minimizing gaps and drafts that can occur with traditional timber framing, leading to better overall thermal performance.
Fire Resistance and Safety
In areas prone to bushfires or for homeowners concerned about fire safety, the choice of construction materials is paramount. MGP timber and LVL both require treatment or protective coatings to improve their fire resistance. While timber naturally has some degree of fire resistance due to its charring rate (which can protect the inner core of the wood for a time), LVL, because of its manufacturing process and the potential for chemical treatments, can be engineered to meet higher fire-resistance standards. Homeowners should consult with their builders and local regulations to ensure their home meets all necessary fire safety standards and consider additional protective measures like fire-resistant cladding or treatments.
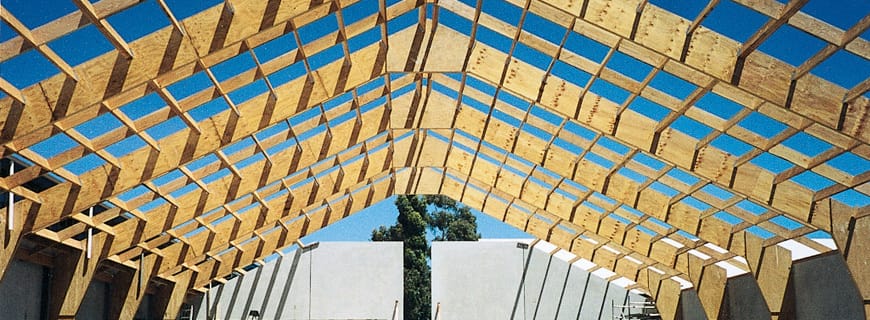
Aesthetic Considerations
The look and feel of a home are crucial for many homeowners, and the choice of framing material can influence the aesthetic possibilities. 90x35 MGP timber offers a traditional warmth and natural beauty that many people appreciate, especially when used in exposed beams or architectural features. It can be stained, painted, or treated to match a wide range of interior styles.
LVL is often chosen for its strength rather than its appearance, as it is typically used in areas that are not exposed. However, when used as a visible design element, LVL can provide a modern, clean look with its smooth, uniform appearance. It can also be treated or covered to blend with the home's aesthetic.
DIY Considerations
For homeowners interested in taking on parts of their construction or renovation projects, understanding the workability of 90x35 MGP timber and LVL is key. MGP timber is user-friendly, easily cut, nailed, or screwed with standard tools, making it a great option for DIY enthusiasts. Its versatility makes it suitable for a range of projects, from framing to finishing touches.
LVL requires more specialized tools for cutting and joining due to its density and strength, which might be a consideration for those without access to professional-grade equipment. However, its dimensional stability and strength can be advantageous for specific projects, such as creating long spans without support columns, offering ambitious DIYers unique design possibilities.
Warranty and Insurance Aspects
Warranties for framing materials can provide peace of mind, covering defects or issues like termite damage or structural integrity. Many suppliers of MGP timber and LVL offer warranties, but coverage details and durations can vary, so homeowners should review these carefully before making a selection.
Insurance companies may also consider the type of framing material when determining premiums. Buildings constructed with materials that have a higher fire resistance or durability might benefit from lower insurance costs. It's advisable to consult with insurance providers to understand how the choice of MGP timber or LVL might affect premiums, especially in regions prone to natural hazards.
Future Trends and Innovations
The construction industry continues to evolve, with sustainability and efficiency driving innovation in materials and building practices. Developments in timber treatment and manufacturing processes are enhancing the performance of traditional materials like MGP timber and LVL, making them more durable, sustainable, and adaptable to a variety of design needs. Emerging materials, such as cross-laminated timber (CLT), are pushing the boundaries of what's possible with wood construction, offering new opportunities for energy-efficient, environmentally friendly homes.
Conclusion
Choosing between 90x35 MGP timber and LVL for framing in Australian residential construction ultimately depends on a project's specific requirements, budget constraints, and long-term goals. While MGP timber provides an affordable, versatile option for many conventional projects, LVL offers enhanced strength, durability, and design flexibility, albeit at a higher initial cost.
Builders and homeowners should weigh these factors carefully, considering not only the upfront costs but also the long-term performance and maintenance requirements of their chosen material. By doing so, they can ensure their construction meets Australian standards and serves as a durable, reliable home for years to come.